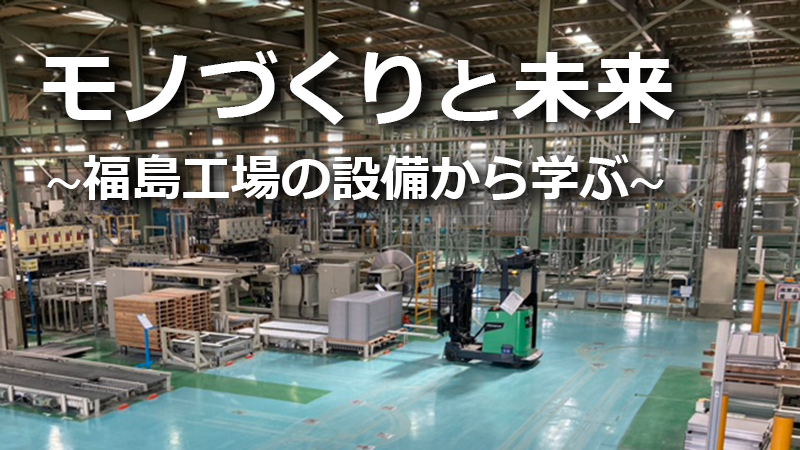
こんにちは!三進金属工業株式会社採用担当の青野です。
アジア最大級のラック生産力を誇る福島工場。
今回は、福島工場の設備をもとに「モノづくりの未来」について、生産技術部 T.Oさんにインタビューした内容をお伝えします!
福島工場におけるモノづくりの自動化
棚板製造ラインの4ラインについては、コイル材カット・穴あけ・フォーミング成型・補強自動供給装置・スポット溶接を経て、完成した棚板を自動集積します。
福島工場は第1工場から第4工場までありますが、その中でも第1工場では、1日あたり多いときには約6,000万枚もの棚板を生産します。
すでに自動化されている部分はあったものの、1日における搬送作業は約120回に及び、大量に生産される棚板の搬送が作業者への大きな負担になっていました。
そんな中で、無人フォークリフト(AGF)を導入。生産ラインから、完成した棚板をAGFが回収し、自動倉庫へ一旦入庫します。
また、次工程の準備が整うと、自動倉庫まで移動したAGFが再び出庫された棚板を塗装ラインまで自動搬送します。
このAGFの導入により生産性向上と搬送時間の削減及び省人化を実現しました。
無人フォークリフト「AGF」
「無人」ということで安全性について気にされる方もいらっしゃると思いますが、それも問題ありません。
第1工場は作業者や有人フォークリフトの往来も多い工場ですが、各種センサーやメロディーフォンなど数々の装備によって安全が確保されています。
AGFは自動倉庫への入庫作業、塗装ラインへの出庫作業を合わせて1日約16時間使用しています。
また、支柱・ビーム製造ラインでも自社製自動集積装置やロボット、全自動ビームガセット溶接機などを使用し、自動化に向けた取り組みを行いながら今後も多様化するニーズに合った新時代のラインを構築していきます。
モノづくりが自動化したことのメリット
こういった自動化設備の導入により、都度、工程負荷が大きいラインやそのほかの部署に人員を充てることが可能となりました。
実際に、棚板製造ラインの4名と塗装ラインへ運搬する1名の計5名の人員が、現在トータルで3名に。
これは、工場全体の稼働率をはじめとした効率化に大きく貢献しました。
福島工場ではほかにも多くの人出を必要とする工程があるため、システムの横展開によってさらなる省人化を図っていきたいと考えています。
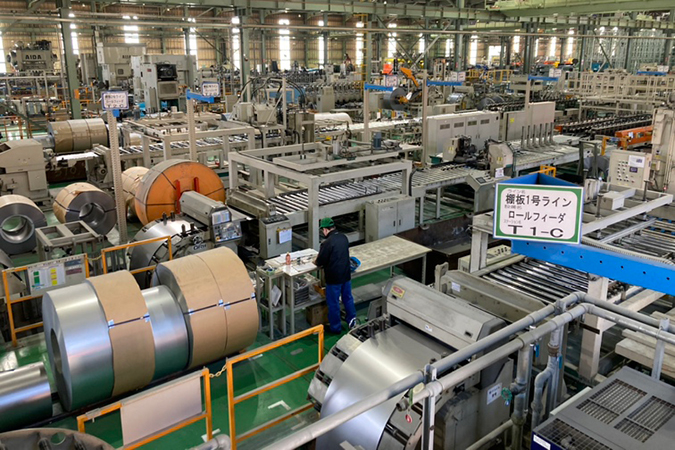
棚板ライン
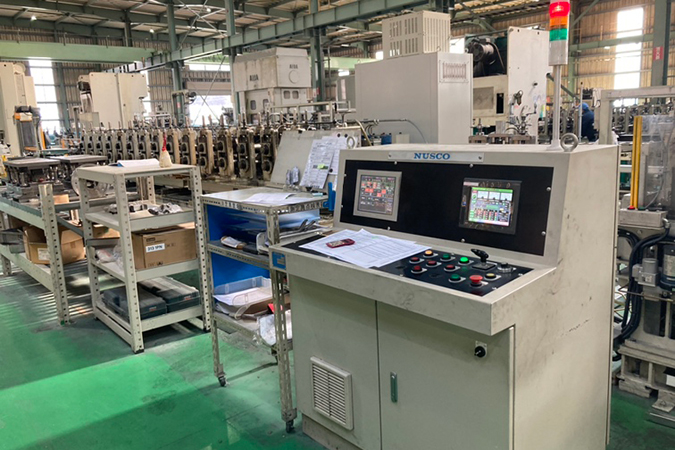
フォーミングライン
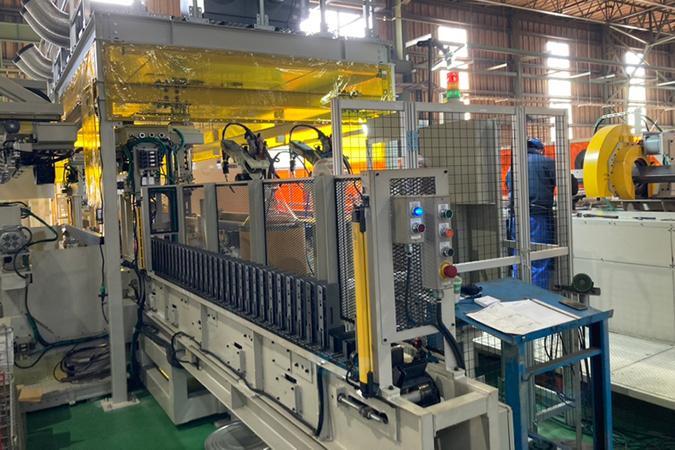
ビームガセット自動溶接装置
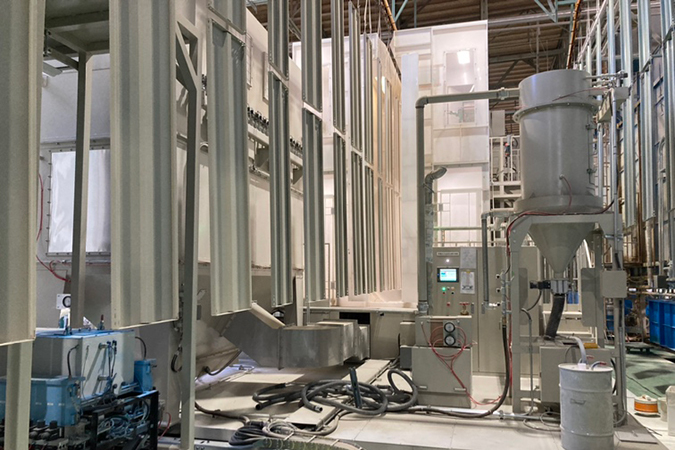
縦吊り粉体塗装機
自動化設備を利用する上で大切なこと
自動化設備を導入することで、複雑な機械操作やそれにともなった知識も必要になるため、オペレーター自身の教育が必須。それに加えてロボット操作などは法規制的な資格が必要になります。
日々設備が進化する中で、自分自身も進化し続けることが大切です。
また、安定的な設備稼働を維持するために、設備メンテナンスをしっかり行うことも重要。怠ると突発的なトラブルが発生し、生産が予定どおり終わらなくなり、納期遅延に繋がりかねません。
自動化によって見えてきた課題
自動化設備の導入により、供給される製品精度が均一でないとうまく次工程に搬送できなかったり、それが原因で製造設備がわずかな時間だけ停止したりするトラブルが頻発することも。
また、前工程でトラブルがあると、次工程のロボット溶接などで正確な溶接ができなくなり、不良品が多くなることもあります。
前工程の既存設備の見直しを検討し、さらに精度を高めていく必要があります。
三進金属工業の未来
三進金属工業は時代とお客様ニーズにこたえるべく、地域と共に未来に貢献する「百年企業」をスローガンに掲げ、現在の人員体制で300億円企業を目指しています。
そのためには、さらなる自動化と生産性、稼働率向上が重要になります。
何事においても素直な気持ちと探求心を持ち続けて共に歩みましょう。
インタビュー記事は以上になります!